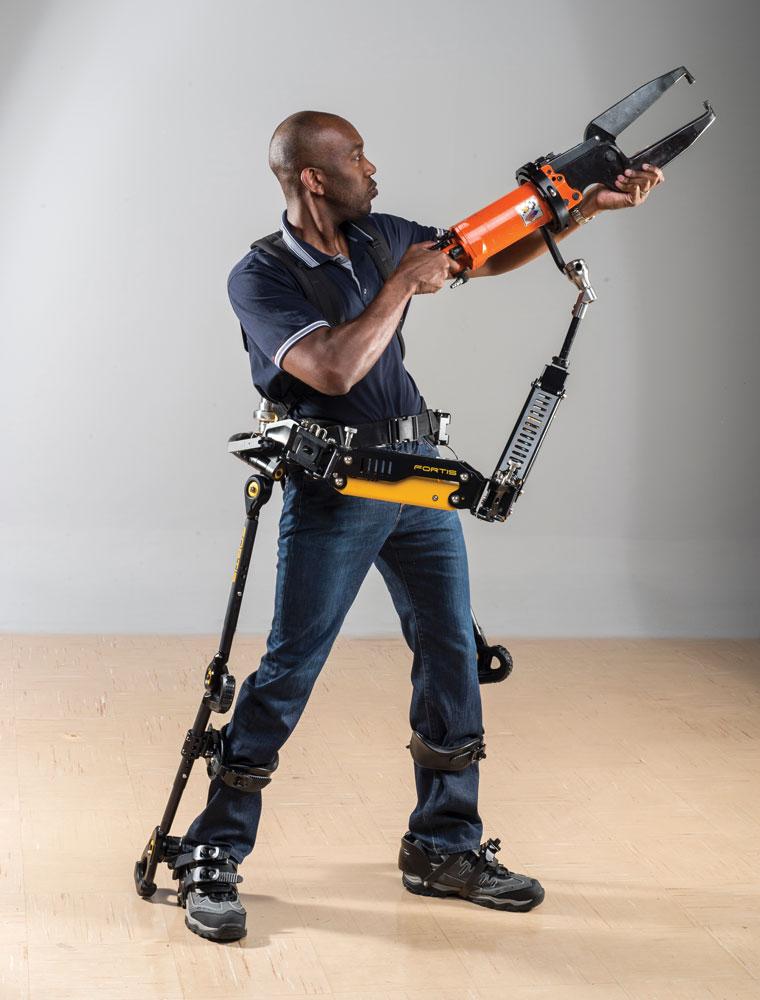
The FORTIS exoskeleton allows the weight of a tool to be transferred to external “legs” that carry that weight outside the body to the ground. This allows an operator to focus strictly on doing his job with precision without having to be concerned with the strain of the tool. Image courtesy of Lockheed Martin.
Work-related musculoskeletal disorders (WMSDs) are a group of painful disorders of muscles, tendons, and nerves. According to the Canadian Centre for Occupational Health and Safety (CCOHS), WMSDs are sometimes inaccurately labelled because most terms don’t explain precisely how these injuries occur. For instance, the term “repetitive strain injuries” suggests that repetition causes these disorders, but awkward postures also contribute to them.
What is indisputable is that WMSDs arise from movements such as bending, straightening, gripping, holding, twisting, clenching, and reaching. The repetition of these movements without giving the body time to recover is what can lead to injuries.
In the past few years, the development of exoskeleton technologies has matured to help companies better equip employees that do repetitive work such as welding or grinding in awkward positions with heavy tools.
Broadly speaking, exoskeleton technology can be broken into two types: units that shift weight to a superstructure below the waist, and those that take the strain off a user’s arms by creating extra support at the hips. In this article we look at an example of each.
Passive Lower Body Support
Some exoskeleton concepts aim to offload weight to allow an operator to focus solely on craftsmanship and the tool he is using to complete a task.
This is how the FORTIS exoskeleton from Lockheed Martin works. The exoskeleton has joints at the hips and knees so that the operator can squat or walk as necessary. It has a multijointed tool arm that is attached above the hip joint where a tool weighing up to 36 lbs. can be mounted.
The weight of the tool, in this way, is transferred to these external “legs” that carry that weight outside the body to the ground.
“This is called ‘passive load transfer,’” explained Gavin Barnes, lead engineer for Lockheed Martin’s Exoskeleton Technologies team. “This is an unpowered exoskeleton, utilizing springs, a rigid structure, and basic mechanics to provide support. And it works with the operator: The user depends on the exoskeleton to give him structural support, whereas the exoskeleton relies on the user’s balance to keep everything upright.”
Passive load bearing is one of two forms of physical support the device offers. The other is upper body balance.
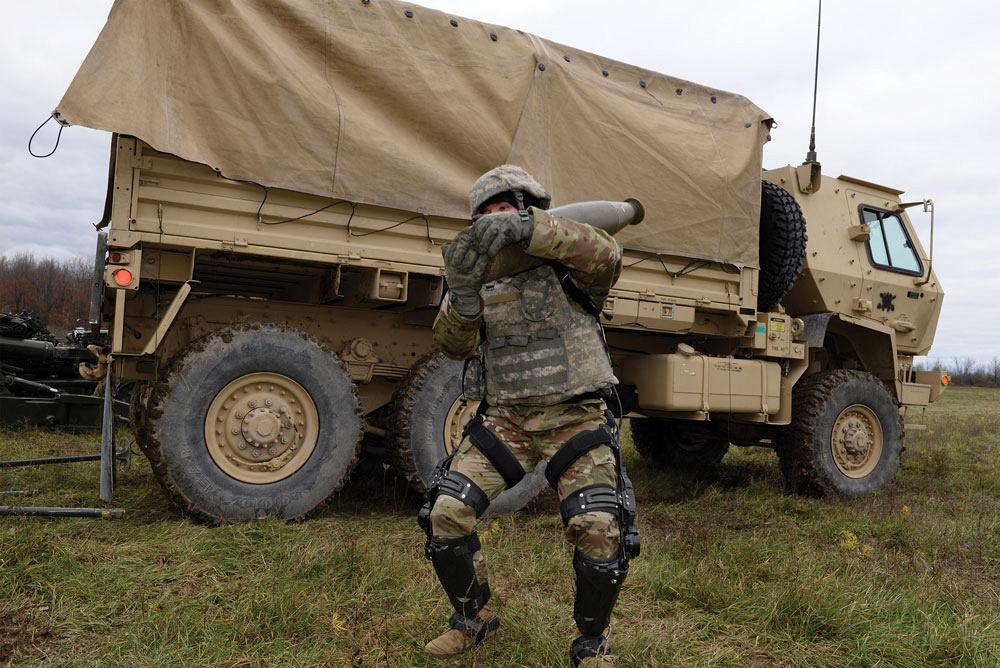
ONYX is a powered exoskeleton based on technology from Quebec-based B-Temia Inc. It combines rigid and flexible structures that conform to the human body. Image courtesy of Lockheed Martin.
“When you are in the proper upright posture, load gets transferred through the frame around the person,” said Barnes. “However, the hips act as a fulcrum while you are working. Without some counterbalance, the tool on the tool arm could easily tilt an operator forward. For that reason, there are a series of weights affixed on the back and the hip joint of the exoskeleton that serve as counterweights.”
It’s critical that the joints on the exoskeleton line up with the human joints they are designed to support, otherwise moving in the device would be difficult and ineffective for the job. For that reason, each joint is adjustable.
“It all comes down to the length of the operator’s legs, but the system could generally be said to suit anyone between 5 ft. 2 in. and 6 ft. 4 in.,” said Barnes.
The tool arm itself can be affixed to an external device such as a bucket lift as well.
“Because it was designed for industrial work, it has a number of safety considerations built in that can be useful when it is operating both on and off the exoskeleton,” said Keith Maxwell, product manager for Lockheed Martin’s exoskeleton business. “For instance, it has a locking mechanism so that if the operator is required to make measurements or check on their work in any other way, the tool arm doesn’t move independently of them. It is also designed to avoid the risk of having any pinch points in its mechanics. And lastly, as it was designed originally for work in shipyards, it is designed to withstand extreme conditions.”
Maxwell stressed that the real cost with a tool like this isn’t the tool at all.
“The real cost is the potential injuries an operator might experience not using this due to fatigue or strain,” he said.
Active Lower Body Support
Lockheed Martin’s focus on exoskeletons is not limited to the FORTIS passive model. In contrast to the passive system, ONYX is a powered exoskeleton based on technology from Quebec-based B-Temia Inc. It combines rigid and flexible structures that conform to the human body. Sensors distributed on the exoskeleton report speed, direction, and angle of movement to an onboard artificial intelligence computer that drives electromechanical actuators at the knees. The exoskeleton delivers the right torque at the right time to assist knee flexion and extension. It ultimately reduces the energy needed to cross terrain, squat, or kneel. These benefits are most noticeable when the wearer is ascending or descending stairs, navigating inclined surfaces, and picking up heavy loads.
The difference this makes for the wearer has proven to be substantial.
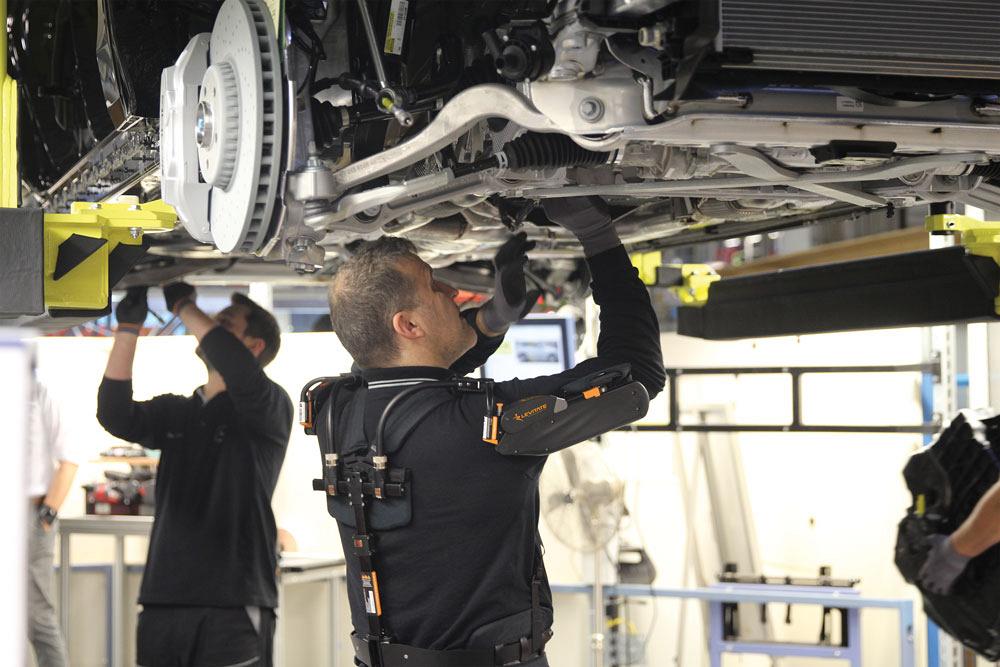
The AIRFRAME system has three main components: a frame, which the user wears like a backpack; cassettes that have pulleys, cables, and springs to provide lifting power; and arm rests that capture and support the user’s arms. Image courtesy of Levitate Technologies.
“We performed a study to try and quantify how much less stress is placed on the human body by wearing this active assist technology,” said Barnes. “In our study, wearers experienced up to a 90 per cent reduction in knee torque when using the ONYX. That makes things much safer for the wearer.”
“We had a soldier, at the beginning of the day, with no assistance, go into the gym and do as many repetitions of a squat with a 180-lb. barbell on him as he could do,” said Maxwell. “He did 22 reps. We then suited him up with the exoskeleton and had him do a variety of training drills to simulate the type of mission he’d be involved in. He then did a 3-km walk back to the gym. After that he got under the same bar as he had in the morning, and we stopped him at 73 reps. Using this exoskeleton, we are maximizing the strength potential in an individual by removing stress in the lower body and back.”
Although the exoskeleton was developed initially for the military, industrial trials are set to begin internally at Aecon and, in conjunction with Aecon, at Enbridge.
Passive Upper Body Support
Imagine working on an automobile assembly line installing exhaust system components or brake lines overhead, or welding overhead off and on throughout the day. These tasks require a lot of lifting of materials and tools all day long.
Sure, some employers rotate tasks, and workers tend to be really good at improvising labour-saving devices, but improvised methods have limitations, safety is always a concern; and in a strictly controlled work environment, they’re not allowed. These are cases in which a system that provides some support for a worker’s arms would be ideal. Levitate Technologies Inc.’s AIRFRAME is one such system.
“The system has three main components,” said Joseph Zawaideh, Levitate’s vice-president of marketing and business development. “It has a frame, which the user wears like a backpack. It has cassettes that have pulleys, cables, and springs to provide lifting power. Finally, it has arm rests that capture and support the user’s arms.”
The frame comes in four sizes, and the arm rests are available in three sizes. Cassettes are available in six force levels that correspond to the task at hand. Its modular design means that the system can be tailored to the user.
Because it relies on a system of pulleys, cables, and springs, it’s self-contained. It doesn’t run on batteries or any other power source, internal or external. When the wearer’s arms are at his sides, the system is neutral, allowing him to use his arms as he normally would. When he lifts his arms, the mechanism inside the cassette creates a progressive mechanical force that compensates for the weight of the wearer’s arms and tools. When he lowers his arms, the system disengages progressively and returns to neutral.
The exoskeleton is Levitate founder Mark Doyle’s sixth invention. A previous development assisted surgeons. While the system for relieving fatigue for doctors was a success, Zawaideh thinks that the AIRFRAME has been accepted more readily by manufacturers.
“Toyota commissioned a study conducted by Iowa State University,” he said. “They used a system of muscle sensors to gather 10,000 points of data per second and determined that the unit does what it was designed to do, relieving stress on the arms and spine and transferring it to the hips,” he said. In this case, spine refers to the entire spine. While lumbar vertebrae tend to be the most susceptible to strains and other injuries, the Levitate unit has been shown to relieve stresses on the entire back and neck. Toyota saw so much value in the unit that it made it standard-issue personal protective equipment (PPE) for workers who work at shoulder level and higher. “It’s PPE, just like safety shoes,” Zawaideh said.
Zawaideh pointed out that the exoskeleton isn’t a single product, but a family of products. The company makes several versions of the exoskeleton for specific working environments and applications. Specialty units include exoskeletons that are fire-retardant, well-suited to manufacturing work such as grinding and welding; units that are electrostatically neutral for painting applications; and frames that are compatible with fall-protection harnesses for working at heights.
Regardless of the specific model, getting the fit just right is critical. The fit isn’t based on overall height, but two critical dimensions: spine length and forearm length. Beyond this, the frame has several adjustments so each wearer can fine-tune the fit, Zawaideh said.
Still, sizing a unit is a matter of precision, a task for which the company provides training. Optimal fit is needed for optimal comfort, and optimal comfort is needed for optimal buy-in.
Stronger or Longer?
Although a common goal among exoskeleton manufacturers is to make a person stronger, Zawaideh pointed out that the AIRFRAME transfers the burden to the user’s hips, so he still bears the entire weight.
“It doesn’t make a person stronger,” Zawaideh said. “It allows a person to be less fatigued at the end of the day.”
For those looking into these tools, that is the key question. Is the company looking to simply ensure that an employee is less fatigued at the end of the day, or does the exoskeleton need to help the employee manoeuvre a larger tool like a spot welder?
Regardless, if employees are required to do repetitive work, particularly out of position or overhead work, these technologies can reduce the risk of WMSDs while making the wearer more productive.
Editor Robert Colman can be reached at rcolman@canadianfabweld.com. Contributing Editor Eric Lundin can be reached at EricL@thefabricator.com.
Lockheed Martin, www.lockheedmartin.com
Levitate Technologies Inc., www.levitatetech.com
"load" - Google News
July 27, 2020 at 06:04PM
https://ift.tt/32X7kVl
Taking the load off with exoskeleton tech - Canadian Metalworking
"load" - Google News
https://ift.tt/2SURvcJ
https://ift.tt/3bWWEYd
Bagikan Berita Ini
0 Response to "Taking the load off with exoskeleton tech - Canadian Metalworking"
Post a Comment