Construction is set to begin this fall on a five-story, mixed-use building in Roxbury. While modest in size, its development could mark the beginning of big changes to how buildings are constructed in Boston and beyond.
The use of what some researchers call a "revolutionary" type of timber promises to reduce emissions that cause climate change, create affordable housing and jumpstart a new job-producing, homegrown industry in New England.
Seeing The Value In The Forest And The Trees
Fallen leaves and branches crunch underfoot as Frank Lowenstein heads into the woods at the Robert Treat Paine Estate in Waltham. Lowenstein, chief operating officer of the New England Forestry Foundation, quickly sees what he’s after.
“I’m looking for a hemlock. … Oh, here’s one,” he says, pointing to a tall, straight evergreen with droopy branches.
The eastern hemlock is the second-most prevalent tree species in New England among billions of trees.
“Eighty percent of the region — 33 million acres — is forest,” explains Lowenstein, who adds that the hemlock is an underutilized, low-quality, low-value tree. It is used primarily for framing houses, pulpwood and rough-hewn pallets.
Lowenstein is excited about recent test results from researchers in Amherst, who hope to put hemlocks to better use by turning the trees into what's called "cross-laminated timber" (CLT). The CLT process takes long pieces of wood and glues alternate layers at 90-degree angles to make huge, thick plywood sheets and timbers. The researchers have shown regional hemlocks and white pine manufactured into CLT can meet construction standards for fire, earthquakes and strength.
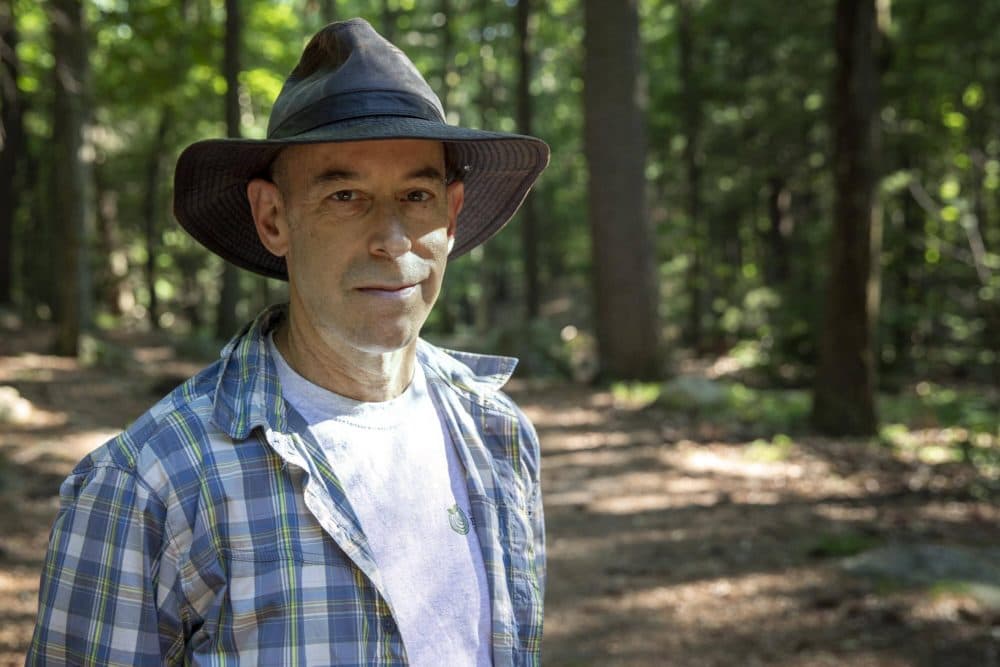
“The University of Massachusetts just made some CLT panels out of [eastern hemlock] and put them into a giant vise to find out how strong they were,” Lowenstein explains, making a crunching sound with his voice to describe the powerful vise test.
Scientists found the wood sandwiches and cross-laminated beams were stronger and lighter than steel and concrete. Those traditional building materials require intense heat to produce, and typically burn coal, emitting enormous amounts of climate-changing carbon dioxide into the atmosphere. After water, concrete is the most used material in the world, and accounts for 8% of human-made emissions. It’s been called "the most destructive material on earth."
Trees, on other hand, capture and store carbon dioxide, Lowenstein says. “Cross-laminated timber is forged from sunlight in the forests, and so there’s a lot lower ... carbon footprint associated with building a cross-laminated building than from steel or concrete.”
Lowenstein believes with the region’s vast forest resources, CLT could become a homegrown industry in New England that could help solve the climate crisis. The technology was developed in Europe in the 1990s, and the tallest timber building in the world is an 18-story tower in Norway. Canada has created several CLT factories, but the technology has been slow to catch on in the U.S.
“We don’t have it here in New England yet, only because [developers] are not convinced there’s enough demand yet," Lowenstein says. "So the first building in Boston is a big deal."
Boston’s First CLT Building
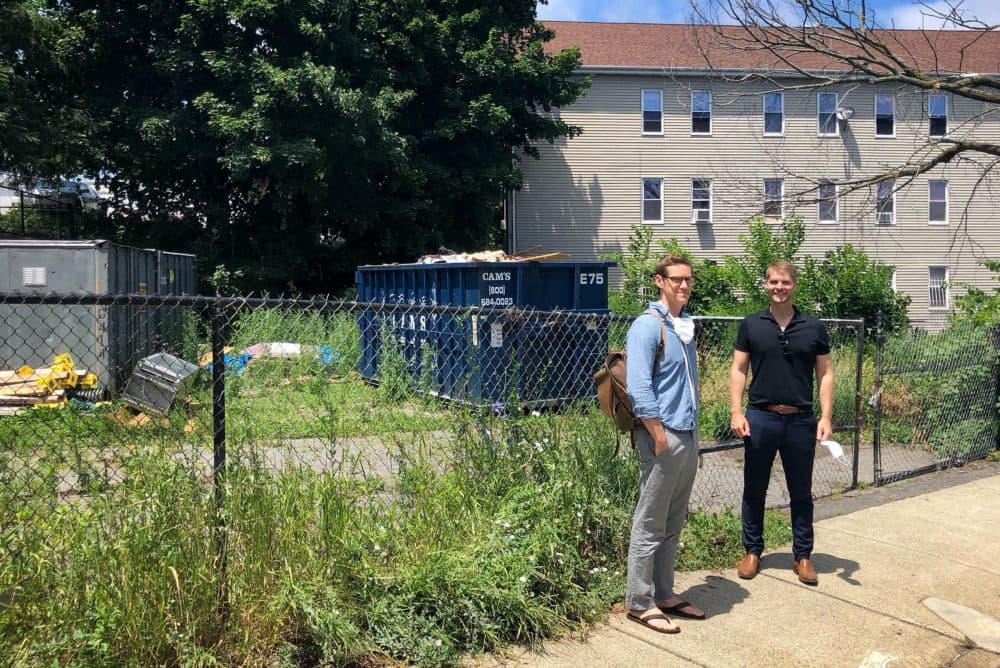
The first CLT building in Boston will be constructed in a small, triangle-shaped lot locked behind a rusting chainlink fence on Hampden Street in Roxbury.
Architect John Klein, CEO of Generate Technologies, stands on the sidewalk in front of the site. His digital design team, trained at MIT, is leading the CLT construction disruption in Massachusetts.
“Yeah, looking at the site, getting excited. That’s the beauty of design,” Klein says. “What you see is dumpsters and weeds and turn it into something magnificent for the area. It becomes a catalyst.”
In a matter of weeks, using cross-laminated timber panels made in a factory in Montreal, Klein’s design will turn this site into a five-story, 14-unit building with ground floor commercial space.
Local Roxbury residents will be trained to assemble the CLT pieces, providing jobs and possibly pathways to careers and homeownership, says Colin Booth, the developer of the Roxbury building. He calls this a demonstration project to test CLT's many transformative possibilities.
“This is going to set the tone for what we are going to build for some time and the rest of Boston, as well," he says.
Booth is Strategic Director at Placetailor. The Boston-based development and design cooperative was started a decade ago by artists and activists. They put together the financing for the CLT building which will be built to energy-efficient passive house design standards. Booth modestly says the company’s mission is to save the world.
“We’re trying to provide a model for how to address a number of the crises happening in Boston right now. There’s a housing crisis in terms of need. There’s a climate crisis that the city needs to do its part in helping to address … and there's a gentrification crisis in terms of sweeping residents out of their neighborhood.”
Neighborhood Transformation Or Gentrification?
In the 18th and 19th centuries, the area where Hampden Street lies was part of the Roxbury innovation district. Melnea Cass Boulevard was paved over the canal that made this a main industrial center. You can still see many of the huge brick buildings that once housed piano and soap factories. There was even a steel maker. Today, it is called the Orchard Gardens neighborhood.
"Let me tell you, it’s a beautiful place to live,” says Valerie Shelley, president of the Orchard Gardens Resident Association, a mixed-income community of well-maintained townhomes, apartment buildings and neatly trimmed parks and lawns.
But, she says, "there are folks who don’t live here who bring drama to our community with the drugs and gangs ... and shootings ... thank God we have not [had] shootings … it hasn’t affected us yet.” She knocks on the wood table in her office repeatedly as she speaks.
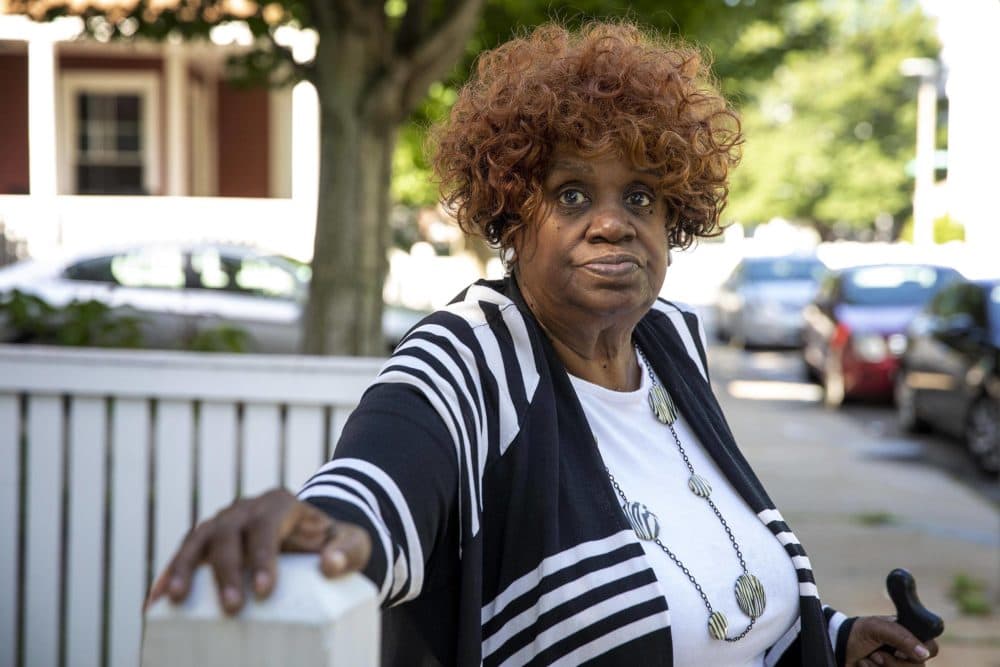
Last year, Shelley met with Klein and Booth. She likes the CLT project and wants to continue the conversation, but she’s worried about gentrification and the affordability of the units in the building.
”What I want them to know ... in their process of development is to talk to the community and see how it affects us," she said. "If they’re not going to help the community, why build here?”
Developer Colin Booth acknowledges that just one of the 14 units will be “affordable” according to Boston’s guidelines, and priced below market.
“It’s not designed to be maximizing for profit … that’s for sure,” he says of the CLT building. "We have to pay back investors, pay back construction loans. This is not a money maker.”
Boston’s first CLT building is designed to demonstrate the feasibility of using the new technology and provide data for future structures. Booth said he hopes the five-story CLT building in Roxbury will be the start of something big.
“This is a learning project. We’re investing in understanding how to do it, and testing it on a scale we can handle," he said. "We wouldn’t want to try it on a 12- to 14-story building as a first. We can manage ... a five-story building and make everything we learn as public as possible so that others can learn and replicate and grow with this model.”
The design and planning process is sort of modeled after Johnny Appleseed, but for urban development, using state-of-the art forest-timber technology, in a Roxbury community.
"first" - Google News
July 21, 2020 at 04:48PM
https://ift.tt/3eMNKxo
In A First, Boston Building Will Be Constructed With 'Revolutionary' Timber - WBUR
"first" - Google News
https://ift.tt/2QqCv4E
https://ift.tt/3bWWEYd
Bagikan Berita Ini
0 Response to "In A First, Boston Building Will Be Constructed With 'Revolutionary' Timber - WBUR"
Post a Comment